New hospital laundry system could help phase out single-use PPE
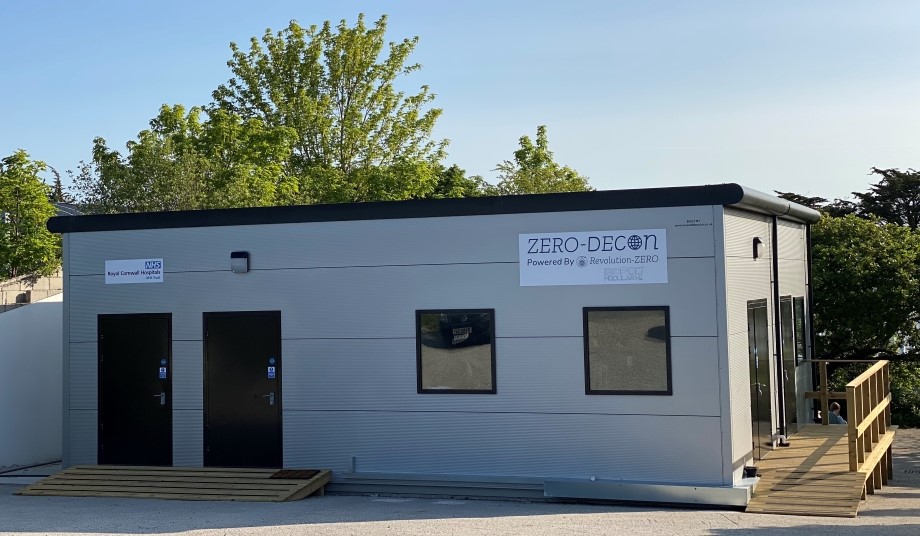
The new laundry system for reusable medical gowns and other PPE items in Newham, Truro
Circular economy experts have made it easier for hospitals to use reusable forms of PPE with the development of a new ‘modular laundry system’.
St Michael’s Hospital in Hayle, Cornwall, is the first to process its reusable facemasks, surgical gowns, operating theatre drapes and other PPE items through the new laundry system, which is located in the Newham business district in Truro.
It was developed by sustainable medical textiles firm Revolution-Zero led by Dr Tom Dawson, a Visiting Research Fellow at the University of Exeter Business School, and funded through private investment and a Small Business Research Innovation (SBRI) contract.
The surgical gowns and operating theatre drapes are designed and certified for 75 reuse cycles, so would go a long way to helping to eliminate medical textile waste.
The existing solution providers for reusable PPE process all regulated medical textiles in large centralised laundry facilities. This centralisation aids industrial efficiencies but can lead to considerable time delays, transport and carbon costs with increasing distance from the centres.
The modular laundry system is mobile and designed for transport by truck. Unlikely traditional concrete and steel builds the modules can be built on site in three months and installed by connection to services in two to three days.
To run the modular units an advanced IT system is used to allow for tracking, training, quality assurance and reporting of asset controls, economic and environmental impact.
The washing and drying machines within the pod have been designed to be as sustainable as feasible by Electrolux Professional and are 100% electric, while the dryers are heat-pump units for added energy efficiency.
Dr Tom Dawson, founder of Revolution-Zero and Visiting Research Fellow at the University of Exeter Business School, said: “The realisation of our first ZERO-DECON medical textiles processing unit in Cornwall is a major milestone for us in our drive to displace, through circular economy solutions, single-use from healthcare supplies in the UK and worldwide.”
As well as the modular laundry system being a model other NHS Trusts could follow, Dr Dawson believes it could also play a valuable role in low and middle income countries where the access to disinfection and sterilization is critical but where supply chains are broken.
He said: “This is just the start of our long-term journey and vision. The value that circular economy solutions can provide is not limited to wealthy nations. We can take the learning from our projects to implement highly effective and relatively low-cost solutions in those global areas that need it most. All going to plan the next few years will be both an exciting and impactful journey.”
Professor Peter Hopkinson, Director of the National Interdisciplinary Circular Economy Hub at the University of Exeter, has helped Revolution-Zero design and develop a full ‘cradle-to-cradle’ life-cycle for its reusable PPE products and described the modular laundry system as a ‘brilliant example of systemic circular innovation’.
He said: “In my opinion it is the best example of a circular economy system design built from scratch. “Everything has been thought through and every challenge and barrier that you can imagine has been overcome, from ensuring the PPE meets the requirements for disinfection and sterilization to demonstrating that it’s a lower cost, lower carbon intensive and lower waste alternative to single-use plastic.”